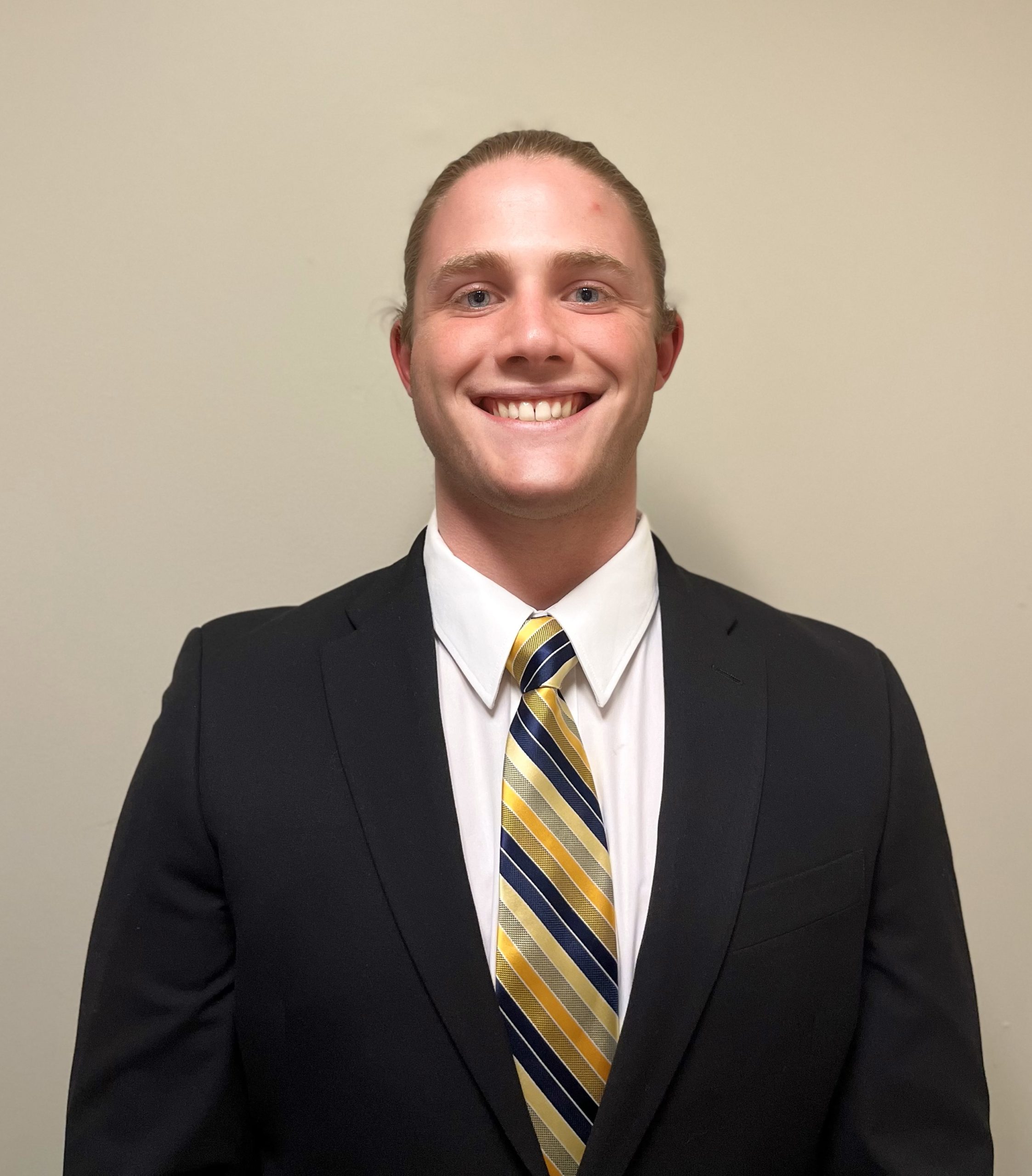
Summer Researcher with Dr. Zubaer Hossain
Mechanical Engineering, Mathematics
University of Delaware
I am a rising junior at the University of Delaware studying Mechanical Engineering with a minor in Mathematics. I am also a member of the University’s Club Rugby Team. After graduating, I plan on using the skills I learned in my time at the University to pursue a career in either the aerospace or automotive industries.
Gavin’s Research Summary:
My research topic for this summer was how effective is AI generative design at improving upon conventional airplane designs, and the area of study in this case was an airplane wing rib.
The first stage of my research involved researching the history of wing rib designs as well as their purpose, as well as reverse engineering a wing rib design to create a 3D model to do benchmarking tests with. There were two 3D wing rib models created, one with a solid interior space, and one with circular cutouts in the interior material, which was found to be one of the most common conventional strategies for reducing weight in wing ribs without compromising their durability. After benchmark stress testing the two wing rib models, the latter wing rib, with the cutouts, proved to be both lighter and performed similarly to the wing rib with no cutouts.
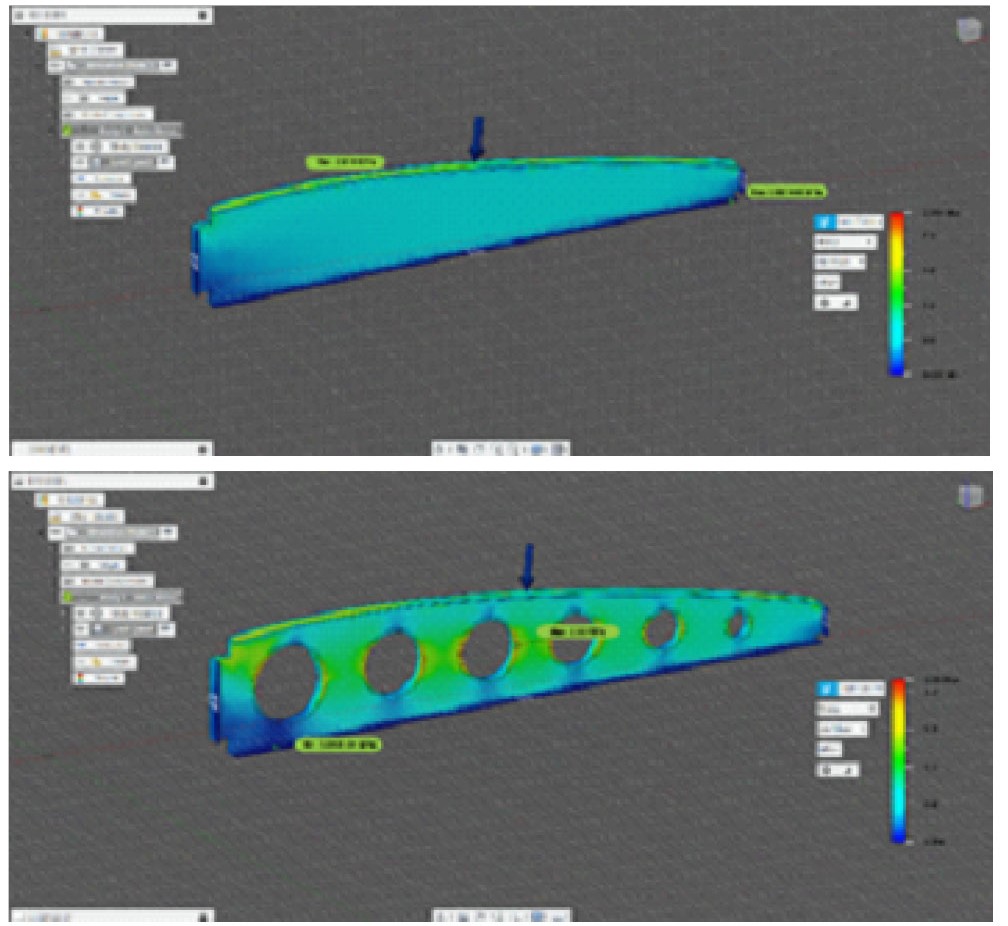
Figure 1: Test image of wing rib with no cutouts (top) and wing rib with cutouts (bottom)
The second stage involved doing background research on AI generative design, which included: how it works, what types there are, and what its main benefits are. During this process I read about topology optimization, which will show designers an optimized concentration of material within a silhouette of their current design, allowing them to adjust and remove unnecessary material from their design in order to reduce material cost and mass. Generative design is different from topology optimization in that it doesn’t simply present a revised topology to the designer, rather it nearly creates new designs from scratch, barring compatibility constraints for the design at hand. It does this by creating many different successive iterations of a design, testing them and adding or removing material as needed, all within a period of a few hours to a few minutes, depending on the complexity of the constraints.
Using the generative AI tool on Autodesk Fusion 360, I removed the filler material from my wing rib designs and allowed the program to optimize the space, resulting in designs that had a 65 to 70% reduction in mass, but comparable or even better strength properties.
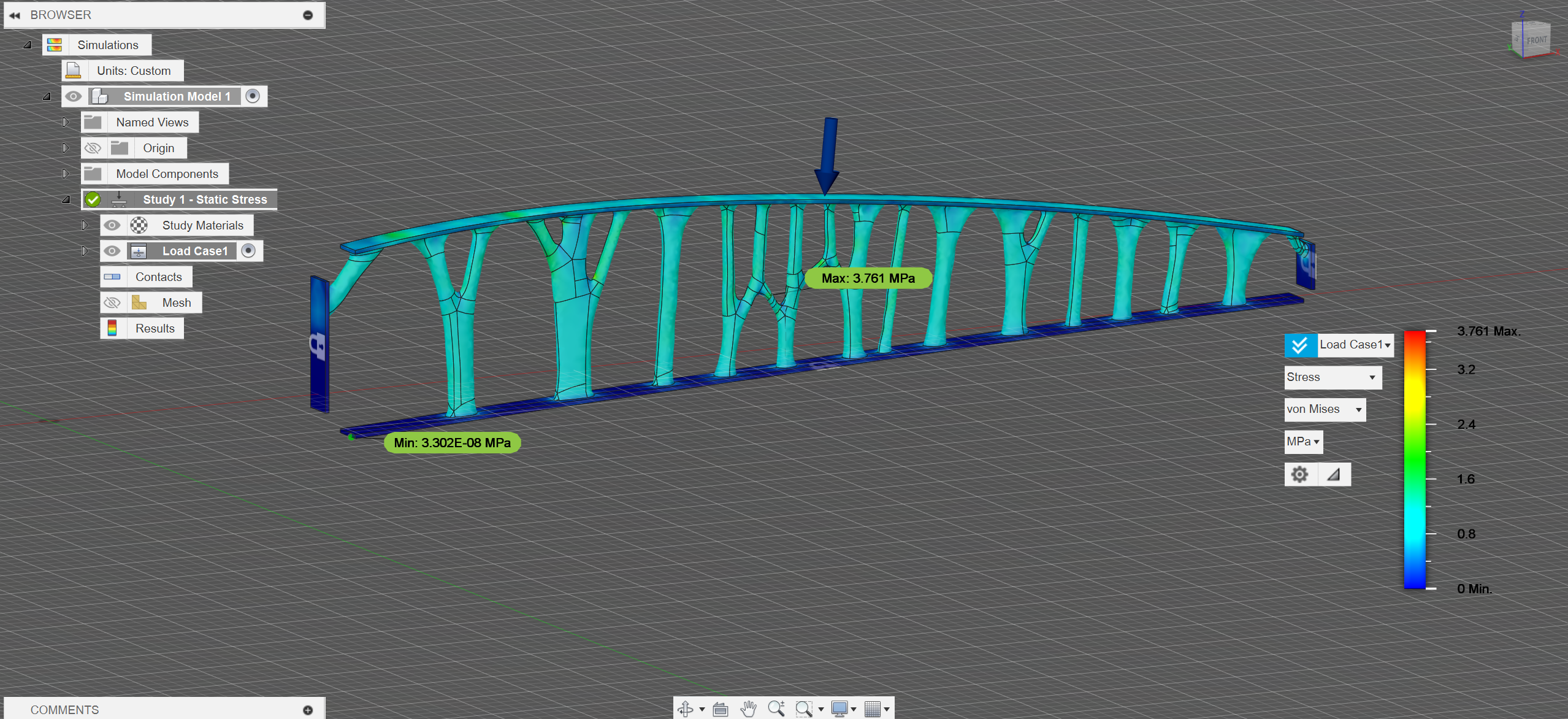
Figure 2: One of the wing rib designs created using generative AI
After finding that Generative AI proved to be proficient in creating lightweight alternatives to conventional aircraft wing ribs, I set out to research possible manufacturing methods that could best recreate these new designs. The methods researched were 3D printing with aircraft grade metals such as aluminum, casting the designs (possibly using 3D printed molds), and machining the parts. While all were feasible options, the conclusion was made that casting, using a mold created from a 3D printed prototype of the wing rib designs would be the most advantageous method, due to the time advantage of a fully realized casting setup over 3D printing and machining, which each take a much longer time to produce a single part. I also made the note that if complex generative designs were to become more mainstream in their usage and production, casting would be the best option due to better capability for increased volume of production and economies of scale.
The final stage of my research involved researching aerodynamic forces to potentially create a better test process and more accurate loading conditions for the wing rib 3D models and subsequent generative AI versions of them, as the original test was fairly simple, given my limited knowledge of aerodynamic forces and fluid flow. The main takeaways from this segment of research were that to create a more accurate test, forces from the air pressure differential on the wing, reactions at the wing spars (components which connect to the wing ribs), torsion along the wing axis, and compression across the span of the wing due to drag would all need to be accounted for. To approximate these forces, either extensive aerodynamic calculations would need to be done or a computational fluid dynamics simulation could be run with a partial wing assembly to analyze the forces on the wing rib within. Due to my limited experience with these subjects (I am taking fluid mechanics for the first time this fall semester), I believe it is a good place to conclude my research until I am either more knowledgeable on the subject or another person that specializes in aerodynamics would be willing to continue.
My research experience this summer was a very fulfilling one, as I got the opportunity to delve into subjects that I considered myself to be interested in, and used the technical ability and knowledge that I have acquired so far in my academic career to find data and draw conclusions on a subject that could potentially help improve an industry. I also found it nice that I ended my research at a place where I haven’t truly learned the next step, so as I take this class this fall, I can consider how I would apply any newfound knowledge that I gain back to the research I did this summer.